石墨轉子對于密度要求是什么?
常用的除氣精煉方法有除氣精煉和噴粉精煉。其原理是將惰性氣體或精煉劑引入熔爐底部。精煉劑很輕,惰性氣體或精煉劑開始從爐底上升。上升過程帶走鋁液中的氫和浮渣,從而凈化鋁液。除氣用的除氣器通過電機帶動法蘭盤,法蘭盤連接石墨轉子轉動。一般石墨轉子使用壽命短,容易被腐蝕壞。為此將石墨轉子浸泡在高溫高壓的介質中,然后燒結固化,提高其使用壽命。這種石墨主要依賴進口,成本高。
旋轉噴粉細化效果好,但容易堵石墨轉子。生產中使用干燥的惰性氣體或高純氮氣進行精煉。氣體連接到法蘭上,法蘭在電機的驅動下開始旋轉。石墨轉子隨法蘭轉速400 ~ 600 r/min,惰性氣體(氬氣)流量控制在15 ~ 25 L/min,氮氣流量控制在20 ~ 40 L/min。在操作過程中,首先打開空氣閥,然后慢慢降低除氣器,直到除氣器石墨轉子與鋼包底部之間的距離為100~150 mm。最后,啟動電機,開始除氣精煉10 ~ 20 min。為了避免石墨轉子高速旋轉產生的鋁液漩渦,在石墨轉子的一側或兩側放置擾流器,以減少旋轉過程中鋁液的湍流。石墨轉子脫氣時保證氣泡細小、分散度高、效果好,既能保證脫氣效果,又能避免氣泡打破表面氧化膜而引起沸騰的現象,從而避免二次吸入。脫氣后,關閉電機,將石墨轉子提離液面,然后關閉空氣閥。由于除氣前在表面加入除渣劑,除氣時產生的鋁渣浮在表面,需要敲出渣灰。用專用工具將瓢中的濾液舀出,建議在液面以下快速平穩地倒入兩個專用坩堝中。一個坩堝在常壓下固化;另一個坩堝迅速蓋上鐘罩,抽真空,真空壓力必須達到8 MPa,抽真空時間為3 ~ 4 min。放入水中冷卻,取出晾干,按常壓測量密度當量后抽真空。密度當量越小,鋁液中的氫含量越低,除氣和精煉效果越好。根據不同產品對密度當量的不同要求,不合格的密度當量需要重新細化。
在鋁合金熔煉過程中,鋁液在精煉前需要進行變質處理。鋁液從熔煉爐轉移到鋼包前,變質劑以合金的形式加入到爐底,變質元素不直接加入。鋁鍶合金棒常用作變質劑。Sr是一種長效變質劑,作用時間為6 ~ 8 h,使粗大的片狀硅細化為細小的組織,力學性能進一步提高。這種改性效果優于將其加入熔煉爐中,并能減少燒損和衰退。Sr爐底熔化后,采用旋轉脫氣攪拌均勻,減少偏析。Sr變質后的鋁液吸氫快,產生許多針孔。精煉后停留時間不宜過長,測氫合格1h以上方可使用。鋁液轉移到鋼包后,撒除渣器,深層攪拌產生渣灰。測量鋁液溫度是否能達到精煉溫度。如果溫度過高,則需要添加回爐料來降低溫度。如果溫度低,就要通電升溫。精煉溫度應控制在720 ~ 740℃。直到調整合格,在表面撒少量除渣劑。脫氣精煉主要涉及脫氣和除氫。由于第一次深攪已經去除了大部分夾渣,但里面還有少量鋁渣,第二次撒少量除渣劑。
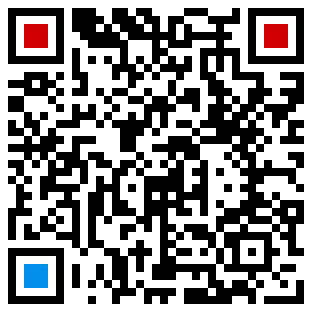
