石墨軸承的具體工藝流程是什么?
石墨軸承的詳細出產工藝流程:原材料——內外圈加工、鋼球或滾子加工、保持架(沖壓或實體)加工——軸承裝置——軸承制品。
在石墨軸承出產工藝流程中,最為要害的是以下幾個環節:
1、鑄造環節
鑄造環節是保證軸承運用可靠性和壽數的重要環節,原材料經過鑄造后,形成軸承套圈毛坯。與此同時,原材料的組織結構變得愈加細密、流線性變好,然后可以提 高軸承可靠性和運用壽數。此外,鑄造工藝的好壞還會直接影響到原材料的利用率,然后對出產成本產生影響。
2、熱處理環節
熱處理環節是將經鑄造、車加工后的軸承套圈進行高溫處理,它直接影響軸承套圈中滲碳的均勻性,可以前進軸承的耐磨性和硬度,也是影響軸承運用的可靠性和壽數的重要環節。
3、磨加工環節
經過熱處理后的軸承套圈還需要實施磨加工,它是保證軸承精度的重要環節。經過磨加工后,軸承套圈的出產進程根本完結。
軸承內外圈工藝流程:棒材——鑄造——車加工——熱處理——磨加工——超精加工——零件終檢——防銹入庫
首要的出產設備包括:冷輾機、全自動球軸承內圓磨床、淬前方、退火爐、壓力機、數控車床、軸承磨床、內溝磨床、外溝磨床、高精度臥軸圓臺平面磨床、數控銑床、無心磨床、高精度通磨無心磨床、精密溝道超精研機、內表面數控磨床、數控往復式雙端面磨床、高溫高速軸承試驗機、熱處理出產線以及質量檢測設備等。
翻滾軸承的根本出產進程
因為翻滾軸承的類型、結構型式、公差等級、技術要求、材料及批量等的不同,其根本出產進程也不完全相同。
一、各種軸承首要零件的加工進程:
1.套圈的加工進程: 軸承內圈和外圈的加工依原材料或毛坯方式的不同而有所不同,其間車加工前的工序可分為下述三種,整個加工進程為: 棒料或管料(有的棒 料需經鑄造和退火、正火)----車加工----熱處理----磨加工----精研或拋光----零件終檢----防銹----入庫----(待合套裝置〉
2.鋼球的加工進程, 鋼球的加工相同依原材料的狀態不同而有所不同,其間挫削或光球前的工序,可分為下述三種,熱處理前的工序,又可分為下述二種,整個加工 進程為: 棒料或線材冷沖(有的棒料冷沖后還需沖環帶和退火)----挫削、粗磨、軟磨或光球----熱處理----硬磨----精磨----精研或研磨----終檢分組----防銹、包裝----入庫〈待合套裝置〉。
3.滾子的加工進程 滾子的加工依原材料的不同而有所不同,其間熱處理前的工序可分為下述兩種,整個加工進程為: 棒料車加工或線材冷鐓后串環帶及軟磨----熱處理----串軟點----粗磨外徑----粗磨端面----終磨端面----細磨外徑----終磨外徑----終檢分組----防銹、包裝----入庫(待合套裝置〉。
4.保持架的加工進程 保持架的加工進程依規劃結構及原材料的不同,可分為下述兩類:
(1)板料→剪切→沖裁→沖壓成形→整形及精加工→酸洗或噴丸或串光→終檢→防銹、包裝→入庫(待合套裝置)
(2)實體保持架的加工進程: 實體保持架的加工,依原材料或毛壞的不同而有所不同,其間車加工前可分為下述四種毛坯型式,整個加工進程為: 棒料、管料、鍛件、 鑄件----車內徑、外徑、端面、倒角----鉆孔(或拉孔、鏜孔)----酸洗----終檢----防銹、包裝----入庫〈待合套裝置〉。
二、翻滾軸承的裝置進程:
翻滾軸承零件如內圈、外圈、翻滾體和保持架等,經查驗合格后,進入裝置車間進行裝置,其進程如下:
零件退磁、清洗→內、外滾〈溝〉道標準分組選別→合套→檢查游隙→鉚合保持架→終檢→退磁、清洗→防銹、包裝→入制品庫(裝箱、發運〉。
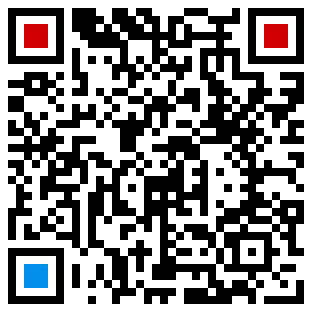
