加工石墨密封圈時操作要點在哪里
加工石墨密封圈時操作要點在哪里
石墨密封圈的加工難度比普通鋼件要大!以上石墨加工的經驗值都是我自己從多年的石墨加工實踐中總結出來的。目前,我的加工方法和工藝已在生產中廣泛推廣應用,提高了工作效率,降低了成本消耗。得到了公司領導的高度評價!目前,我國石墨加工水平與國外仍有較大差距。隨著科學的發展,石墨制品以其自身的特點和低廉的價格在密封產品中得到了廣泛的應用。以上缺點請改正!相信通過我們不斷的努力和學習,我們會有更先進的加工方法和工藝,一定會超越國外的石墨加工水平。
刀具材料及其在生產中的應用
1.石墨密封圈加工對刀具的要求
刀具磨損是石墨加工中最重要的問題,磨損量不僅影響刀具壽命、加工時間和加工質量。而且影響工件加工的表面質量,這是優化高速加工的主要參數!石墨磨損刀具的主要區域是前刀面和后刀面。刀具在前刀面與破碎切削區之間的沖擊產生磨粒磨損,切削沿工件表面滑動產生摩擦磨損,因此加工石墨的刀具必須具有良好的耐磨性。
2.切削工具材料
材料是決定刀具切削性能的根本因素,對刀具的加工效率、加工質量和使用壽命有很大影響。工具越硬,耐磨性越好,硬度越高,沖擊韌性越低,越脆。硬度和韌性是相對矛盾的,這也是刀具材料要克服的一個關鍵。對于石墨刀具,如果產品單一,結構簡單,可以批量生產使用普通的TIAIN涂層刀塊,選材可以適當選擇韌性相對較好的,即鈷含量較高的。對于鍍有細鋼石的石墨刀具,硬度可以選擇相對較好的硬度,即較低的鈷含量。對于多種產品和復雜結構,可選用通用硬質合金刀具。它的優點是流動性強,可塑性強,但缺點也很明顯,磨損很嚴重!需要經常磨刀工具。實踐證明,YG3X硬質合金刀具硬度高、耐磨性好、有一定的沖擊韌性,且價格低廉,基本能勝任加工大部分石墨制品,適合一般工廠加工要求。
3.切削工具的幾何形狀
石墨刀具很容易選擇合適的幾何角度,有助于減少刀具的振動,石墨也不容易倒塌。使用輔助前角加工石墨時,刀具刃口強度更好,耐摩擦性和抗沖擊性更好!隨著前角絕對值的減小,后刀面磨損面積變化較大,但前角一般呈減小趨勢!使用正前角加工石墨時,隨著前角的增大,刀具的切削刃強度減弱,導致刀具后刀面磨損增加,切削刃強度降低,后刀面磨損面積逐漸增大,刀具切削振動增大。經過多年的實踐,發現石墨車刀的正確角度為前角1-3°,前角8-10°(切槽不要磨)。
4.石墨切割機在實際生產中的應用
(1)圓柱車刀:由于石墨被切割成粉末,所以在切割過程中不用考慮切割會劃傷工件。為了提高生產效率,在車刀和機床有足夠剛性的基礎上,不需要粗車直接精車,但切削深度不宜過大(一般以7MM為宜)。但是對車刀的安裝角度有很大的要求。角度太大容易切割,角度太直容易切割產生廢品。一般情況下,車刀是相對卡盤安裝的。
(2)切刀:能否成功切下環形石墨圈,對石墨加工意義重大!它不僅影響產品的廢品率,而且直接影響加工效率,因為石墨環切斷時容易出現邊緣鋸齒和掉渣。以往采用外切法切斷石墨環,但在實際應用中并不理想,加工速度太慢,刀具刃磨復雜。刀具不快時,單邊切削時工件脫落。從而產生廢品!現在改進的方法是:直接用劍切割,使切割的工件內角有保護角,克服了鋸齒邊和崩齒現象,提高生產率60%以上。具體刀具角度為(如圖):尖角最好打磨成90°的形狀,前角為0°,后腳刃打磨成6°-8°,輔助后角為2°-3°。磨的時候,要盡力。但不能太大,要肉眼看得見,0.1MM-0.2MM左右,刀具寬度要在2.5MM-1.5MM,否則會使切割更容易推出工件。
(3)45°圓弧車刀:這種車刀廣泛用于石墨環形工件的加工。由于石墨材料特別脆,加工光軸和通孔時平截面容易崩角,所以通常采用“軟接觸”方式進行切削,即一端倒出30°左右的角度作為過渡毛坯刀具,另一端使用另一種車刀。但是這種方法使用起來太繁瑣,影響了處理效率。通過實際應用,用圓形車刀直接車削也能達到上述效果。而且更快。效率可以提高30%左右。一般圓車刀的R角需要磨到R5到R7之間。(太多會增加切削力;如果太小,圓弧過渡不夠,容易造成崩牙。)加工時,精車的切削量小于1MM,進給量為0.141MM-0.175MM
1.石墨是一種固體自潤滑材料,具有自潤滑性、耐高溫、抗氧化、熱膨脹系數小、摩擦系數低、密度小、可加工性好等特點。可在高速、高壓或低速重載干摩擦的工況下或水、油、氨、丙烷、酸、堿、鹽等介質下工作。石墨因其優異的性能得到了廣泛的應用。同時,石墨的生產和石墨零件的加工有著越來越廣闊的市場空間。
2.石墨是一種脆性材料。雖然很容易切割,但是作為密封端面的石墨材料必須有足夠的強度!為了避免在裝配過程中被損壞,薄壁、尖角等零件的形狀也要求石墨具有較高的晶粒度和強度。這些因素導致石墨工件在加工過程中易碎和破裂。
3.由于石墨材料的特殊性,在實際生產中很難保證石墨制品的加工精度。特別是普通硬質合金車刀在加工時,每100 MM可磨損約0.05MM-0.08MM,表面容易掉渣,所以往往需要進行磨削,以滿足切削、切削精度和表面粗糙度的要求。然后,由于材料的脆性和高硬度,出現崩角、邊緣參差不齊等現象。在車削光軸、通孔、平端面和切削時容易發生。所以相對于鋼材加工,難度大大提高。
3.普通車床車削石墨切削參數的選擇
由于石墨晶粒較硬,如果切削量選擇不當,會對加工產生影響。
1.切削速度:用YG3X硬質合金車刀車削石墨密封環時,主軸轉速不宜過高,會加快刀具磨損,轉速過低則達不到光潔度的要求。一般選擇560/min-280/min,根據工件周長確定。
2.切削深度:石墨與鋼相比密度低,粗加工時切削量大,最大切削量可達單面10MM。但對于薄壁工件,為了避免擠壓壓壞工件,切削量不容易過大,一般5MM-6MM為宜。
3.進給量:石墨材料的晶粒較硬,特別是用硬質合金車刀切削時,進給量不能太大,會因擠壓導致加工表面出現“麻點”和形狀缺陷,造成表面光潔度不夠,產生廢品!如果進給速度過小,會影響加工效率,延長刀具的車削時間,使刀具磨損。以下是我這些年積累的經驗值,如圖:
制品技術規格
()加工表面進給速度MM(單面)進給速度(mm/r)主軸轉數(r/min)
粗車,粗車,粗車,粗車,精車
外徑≤外徑3-10 1-3 0.241 0.175 350 560
內孔2-5 ≤ 0.5 0.175 0.175 350 560
2-5 ≤ 1 0.483 0.483 350 560
≥外徑≥
外徑3-10 1-3 0.241 0.175 180 450
內孔2-5 ≤0.5 0.175 0.175 180 450
端面2-5 ≤ 1 0.483 0.483 280 450
3.加工石墨密封的裝夾和薄壁零件的加工。
(1)石墨密封圈:這些工件大多有壁厚。
(2)步驟多。用傳統的三爪卡盤車削是非常困難的。
(3)夾緊時,容易被折斷。如果用夾具裝夾太繁瑣,工件需要多次裝夾,浪費時間,降低工作效率,實踐證明應采用自定心六爪卡盤。六爪卡盤六點接觸時接觸面積大,受力均勻,定位好。可以多次裝夾,具有多個基準面,保證了工件的形狀和位置公差,適用于加工各種復雜零件。
薄壁零件的加工:一般來說,工件用六爪卡盤夾緊。當壁厚為5MM時,容易破碎,形位公差難以保證!車削時最好兩次切削,防止過度擠壓造成工件應力,保證車刀的鋒利度,保持卡盤10MM為宜,安排合理的工藝,選擇正確的車削方法。
1.用六爪卡盤夾住坯料,將其對齊,旋轉\u 99.7 \u 81至尺寸。應盡可能采用二次切割來加工粗糙的車內孔,以防止石墨在切割過程中產生應力和開裂。
2.切掉總長8MM,留下總長2MM,卡¢97.7圓柱車¢93.4。
3.裝夾¢93.4,車削總長到7.4MM,車削¢91到尺寸,車削¢94到尺寸,采用徑向切割。
4.裝配工鉆孔,小心處理防壓碎,孔深5.8毫米,最薄處不小于1毫米。
5.找到正夾,轉5.4到尺寸,用90°車刀沿軸向轉兩圈。
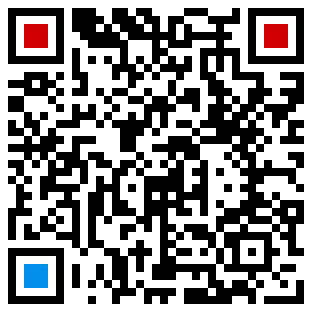
