石墨板的刷釉和燒成過程 ?
經風干后的石墨板,應按半成品加工規范開展檢測。合格品進到涂釉工藝流程刷涂釉料,釉面凝結后可以裝窯和燒制。燒制的目地,是以便提高坩禍的相對密度和沖擊韌性,提高產品品質。
石墨板在燒制全過程中,坯體的安排架構發生一連串改變,改變很大的要害是延展性的耐火粘土。相關石墨板燒制的根底全過程,分為下列4個環節來表明:
(1)加熱烤制環節。窯爐溫度在150-400℃,是高純石墨板坯體鏟除殘留水份的全過程。窯頂全景天窗應翻開,提高溫時速率反映緩慢,非常是當石墨板中殘留水份超出3%時,應嚴控溫度,不然易發生石墨板裂縫和炸罐安全事故。
(2)超低溫燒制環節,350-700℃。系石墨板煅燒的超低溫環節。隨之窯溫的上升,石墨板中的束縛水剛開始溶解和鏟除。黏土中的行為主體成分A1203和Si02,—度發生礦酸情況。石墨板外表釉面并未熔融,提溫速率仍應緩慢開展,假使提溫速率過快和不勻稱,相同也易發生炸罐和塌垛安全事故。
(3)中溫燒制環節:800-800℃。這時候,黏土中非品形A1203, 將會一部分轉換成y型結晶體A120。在窯溫逐步上升的情況下,以礦酸情況而存有的Al208和Si02,便結介成硬實的鋁硅酸鹽的干固物(別稱石油化工全過程),把石墨板中的高純石墨,水泥熟料聯接干固為總體。先在溫煅燒全過程中,石墨板的外表釉面隨之溫度的上升慢慢融化,發生一層層玻璃狀的釉膜,封閉式或遮蓋于石墨板外表,維護著石墨板沒受空氣氧化。這期內提溫速率應快,窯中火苗以還原焰為宜。
(4)高溫燒制環節:此環節溫度為1500-1500℃。這時石墨板中的黏土經中溫煅燒發生干固后,逐步向莫來石轉換,如3A1203+2Si02=3Al203 *2Si02 (莫來石)。這期內提溫速率應該比中溫時加速(別號放火災全過程),窯中火苗應操作為弱酸性焰或還原焰。石墨板在高溫煅燒全過程中,釉面已完全熔融,發生玻璃狀釉膜,封閉式于石墨板外表。若煅燒溫度超過釉料最大溫度底限,易流脫導致石墨板的空氣氧化。因此,在高溫煅燒全過程中,應留心觀查石墨板釉面熔融情況,避免由于過燒而達不上煅燒的目地。
莫來石 (3Al203*2Si02),系這種物理化學特性平穩的高級防火資料礦物質。相對密度、強度、耐火度及其載荷變軟點都很高,線膨脹系數小。在石墨板的安排架構中,起著要害的同結硬底化及承荷成效。由此可見,在石墨板煅燒全過程中,由于延展性耐火粘土的熱電效應成效,把高純石墨、水泥熟料土體為具備有必要的沖擊韌性的總體。因此,煅燒溫度的高矮,操作流程中的溫控,對石墨板產品的質童和使用期,具有電要的危害。
石墨板中的高純石墨,雖具備導電性、熱傳導和耐熱等特點,仍當溫度在800-750℃時,經與氣體長期觸碰,易空氣氧化轉化成CO2。這種行為,雖較為緩慢,但隨之溫度的上升和時間的增加而加速。怎樣維護石墨板在煅燒全過程中高純石墨沒受空氣氧化,在65年代前系選用防火資料硅板搭槽,焦碳末作保護膜(匣缽套燒),密閉式簡接暗火煅燒。這類煅燒方法的要害缺陷是能耗大,窯爐利用系數低,勞動效率大,生產率低,經濟發展高效率差。由于所述難題,我們經科學研究,選用低溶點的釉料與其他原資料相互配合,配置防氧化抗腐蝕釉料,維護石墨板在煅燒 全過程中沒受空氣氧化,從而變革立異了過去的喑火烤共同用火燒結法。這一重特大的加工工藝變革立異,不但提高了石墨板的煅燒質M,而且獲得了不錯的技術經濟實際效果。
(1)石墨板釉料的制?。河粤蠚w屬于這種低溶點化學物質。最開始的釉料是選用工業生產硼砂與低一級黏土熔融而成,后經變革立異選用碳酸氫銨與廢夾層玻璃熔制而成。經變革立異后的釉料,經濟發展可用成本費便宜,具有同硼砂釉料相同 的實際效果。根據相互配合占比,把混和勻稱的原資料放置石墨板中蓋好,石墨板釉料的幾類秘方在爐中開展加溫熔化,保持溫度控制在1200℃上下,時刻約1.6-2h。待熔融物完全無液體物以鐵棍,沾取滴出為度,隨后倒入水冷卻后以水激碎。熔融完好無缺的釉料呈通明色性脆的玻璃體,以松黃、棕褐、淺綠色為宜。經破碎后檢測,在700-63℃:微熔,800-750℃:全熔,合乎石墨板柚子配置的根底規則。
(2)柚子的刷涂,釉料經石碾破碎低于130目,按照釉料制造混和勻稱,調為鉆井泥漿只能用以刷涂。刷涂時,最先消除石墨板外表的泥塵。用刷子沾取釉漿上下左右刷看一遍,再橫刷看一遍。隨后沾取釉漿少數,抹平刷光,保持柚子遮蓋均勻。釉面薄厚在1.6-2mm,每號石墨板均值耗釉泥約12g上下,經涂釉后的坩禍,釉面不行有麻眼,開裂和殘缺不全良莠不齊等缺陷。經預干后可跳過刷口 ,待口部硬固后,可涂一層層防火資料鉆井泥漿,避免石墨板在煅燒全過程中,互相黏連或因口部凹凸不平而透氣性空氣氧化內部。
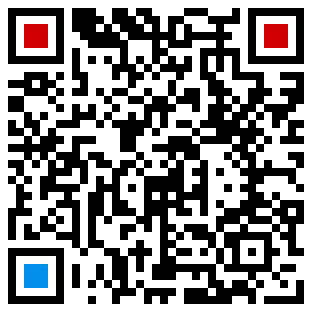
